Rework, rework, and rework are some of the worst words you can hear in manufacturing. Any time packaging or material has to be handled unintentionally a second time, we call it rework. Rework can be generated by many causes and often those causes are linked together. A few of the most common causes are equipment, quality, and speed.
You Must Calibrate and Optimize your Equipment
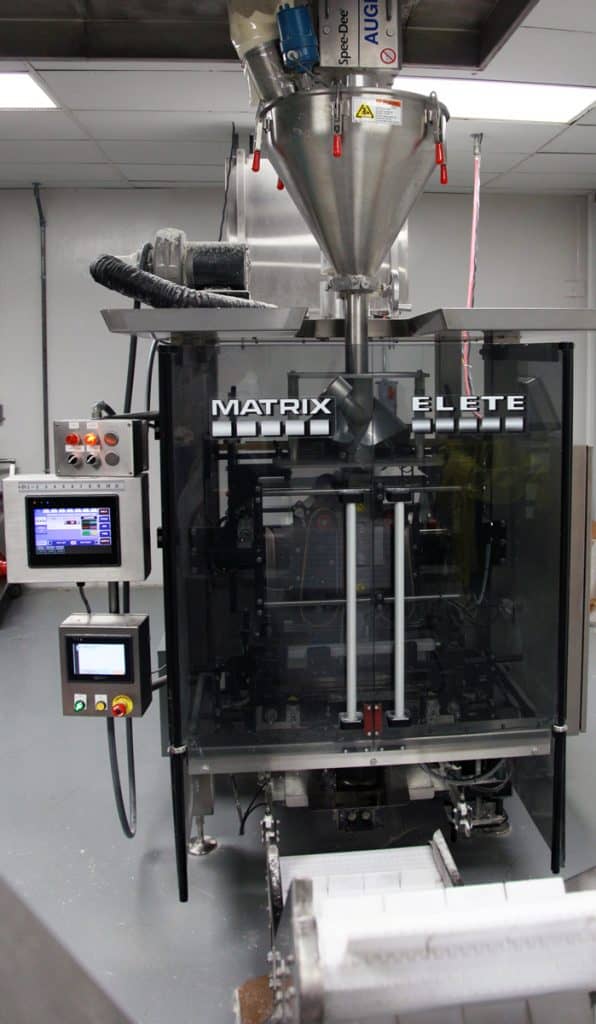
Match Up the Right Packaging with the Right Weight Tolerance
In spec products can vary within a certain weight tolerance so it is important to set the range correctly. A weight tolerance that is overly generous yields waste from product giveaway, while a weight tolerance that is too tight will yield rework and packaging losses due to high amounts of products that weigh less than the minimum weight spec. It is also a critical step to identify if the equipment is worn, in disrepair, or incorrectly sized to avoid this type of rework. Ultimately, if the equipment is correct, the weight tolerance can be adjusted to a preferred range, thus minimizing rework.
Don’t Underestimate Your People
Speed is another cause of rework. Sometimes equipment speed can be a problem, but the operators’ performance should never be underestimated. Working conditions, clear instructions, and proper training can eliminate rework. Setting reasonable, achievable, and profitable production standards create a productive and rework-free performance.
Efficiency is not something that just happens; rather it is achieved by combining efforts and working collectively towards solutions that include proper equipment, good quality guidelines, speeds that are properly managed, and a good training program.